In the ever-evolving landscape of industrial innovation, precision and reliability are non-negotiable. Whether you're designing cutting-edge electric vehicles, optimizing aerospace components, or perfecting consumer appliances, the tools you use to test and refine motor performance can make or break your success. Enter the world of hysteresis technology—a silent force driving accuracy, durability, and efficiency across industries.
🌪️ **Hysteresis Brakes: The Unseen Guardians of Control**
Hysteresis brakes are the unsung heroes of mechanical systems, offering smooth torque control without physical contact. Unlike traditional friction brakes, these devices use magnetic fields to generate resistance, eliminating wear and tear. Imagine a wind turbine adjusting blade speed in gusty conditions or a robotics arm executing delicate maneuvers—hysteresis brakes ensure seamless operation, reduced maintenance, and extended lifespans.
Key advantages:
- Contactless operation for zero mechanical degradation
- Consistent torque across varying speeds
- Ideal for high-precision applications like medical devices or semiconductor manufacturing
🔬 **Hysteresis Dynamometers: Measuring Excellence, One Revolution at a Time**
When it comes to validating motor performance, hysteresis dynamometers set the gold standard. These systems simulate real-world loads with surgical precision, allowing engineers to measure parameters like torque, RPM, and power output under controlled conditions. From EV manufacturers testing battery drain in extreme temperatures to appliance brands ensuring whisper-quiet dishwasher motors, hysteresis dynamometers deliver data you can trust.
Real-world application spotlight:
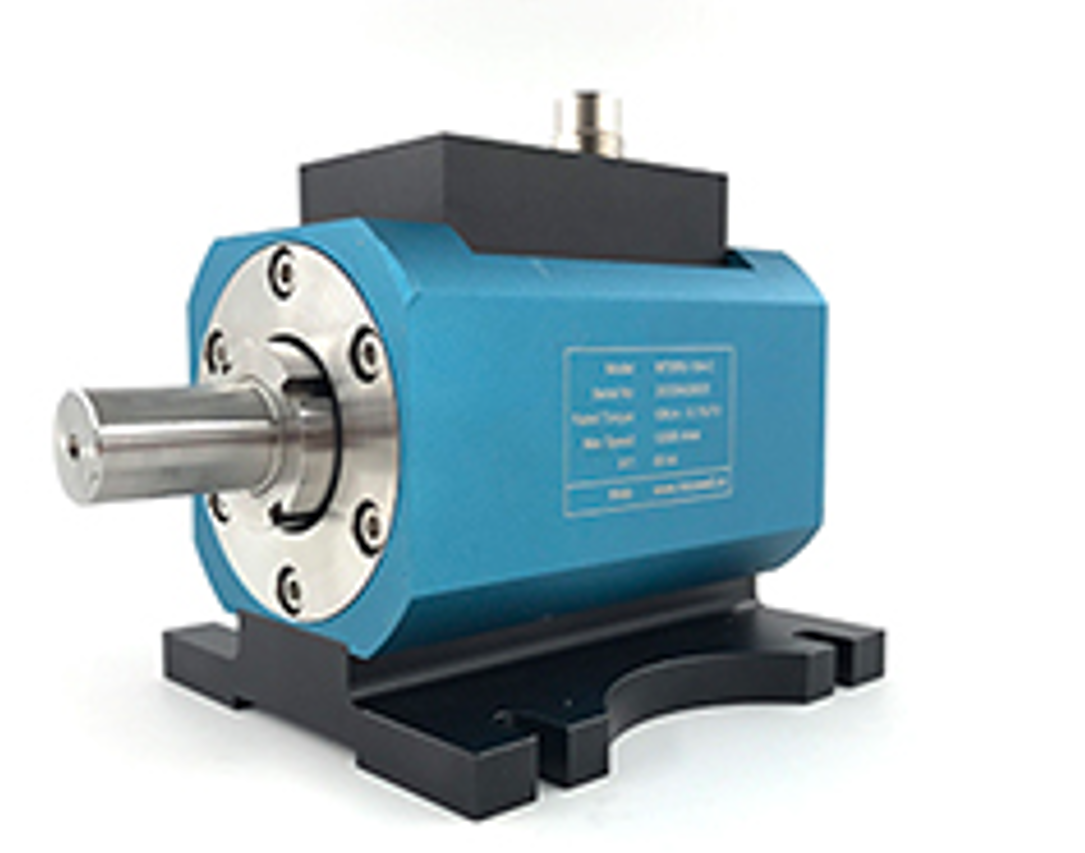
A European automotive supplier reduced development time by 40% using hysteresis dynamometers to simulate uphill drives and emergency stops for electric powertrains.
🤝 **Hysteresis Clutches: The Art of Intelligent Power Transfer**
Blending the precision of hysteresis braking with proactive power transmission, hysteresis clutches enable seamless engagement in applications demanding variable speed control. Picture a packaging line where conveyor belts must synchronize with robotic arms, or a renewable energy system managing power flow between solar panels and storage units—these clutches adapt instantly while preventing mechanical shock.
Tech edge:
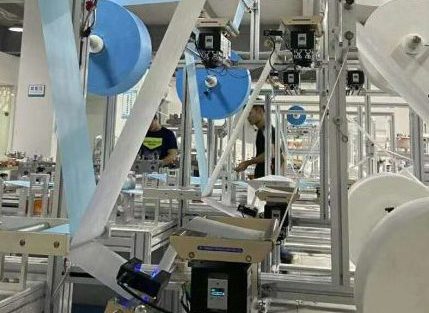
- Non-contact torque transmission
- Immunity to lubrication issues
- Built-in overload protection
⚡ **Motor Dynamometers: Beyond Basic Testing**
Modern motor dynamometers are no longer just measurement tools—they're comprehensive analysis platforms. Advanced models integrate with AI-driven software to predict maintenance needs, optimize energy consumption, and even suggest design improvements. The latest iterations can test motors ranging from micro-drives in smartwatches to 10MW industrial giants, all while collecting data at 100,000 samples per second.
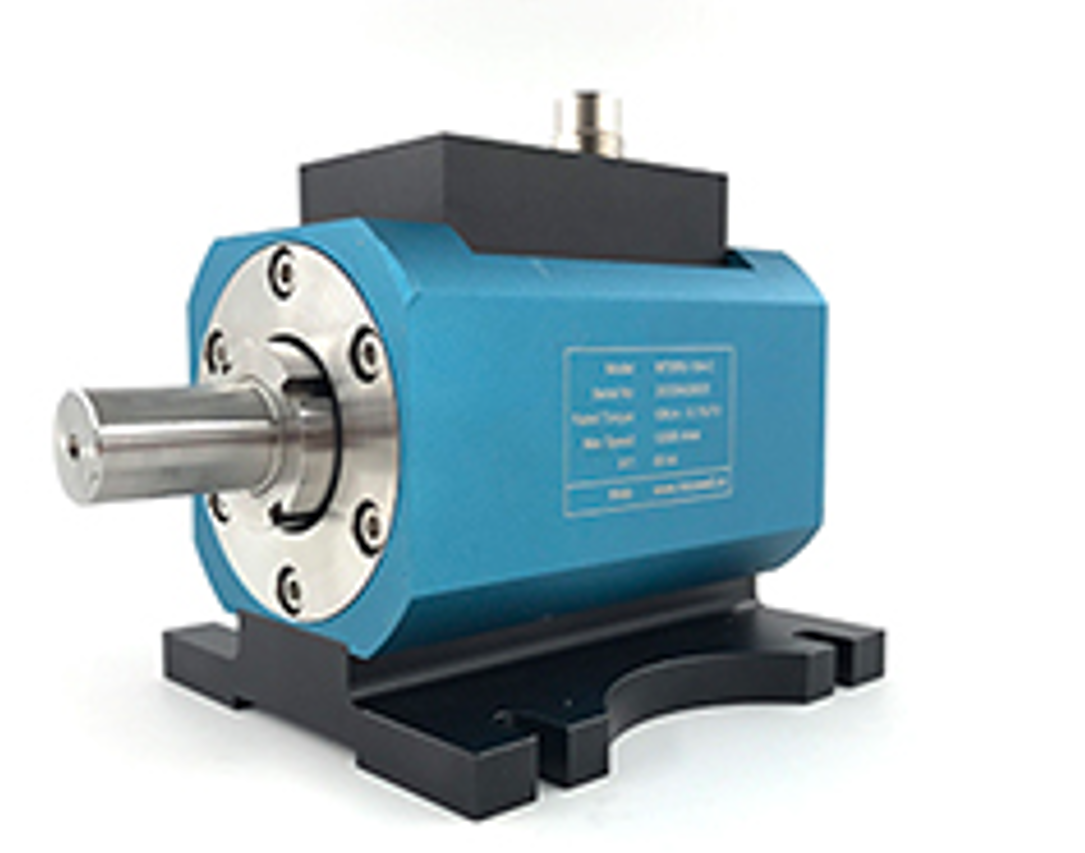
Case in point:
A drone manufacturer achieved 30% longer flight times by using motor dynamometer data to redesign rotor blade angles and stator windings.
🧩 **Motor Test Equipment: Building Blocks of Innovation**
Today's motor test systems are marvels of modular engineering. Imagine a configurable setup that can switch between testing a 500W e-bike motor and a 5,000HP locomotive traction motor within hours. With smart sensor arrays and IoT connectivity, these systems don't just collect data—they contextualize it, comparing results against global databases to benchmark performance.
Features redefining testing:
- Wireless load cells with 0.01% accuracy
- Built-in EMC/EMI testing capabilities
- Augmented reality interfaces for remote diagnostics
🌐 **Integrated Motor Test Systems: Where Data Meets Destiny**
The true power of modern testing lies in integration. Motor performance data analysis where hysteresis brakes, dynamometers, and IoT-enabled test rigs work in concert. Data flows from a motor undergoing climatic chamber tests (-40°C to 150°C) to simulation software, then to 3D printing systems that overnight produce optimized prototypes. This closed-loop ecosystem is accelerating R\u0026D cycles from years to months.
Industry transformation stats:
- 68% reduction in time-to-market for appliance motors
- 92% accuracy in predicting field failure rates
- 55% energy savings in production testing processes
🔮 **Future-Proofing with Hysteresis Tech**
As industries march toward electrification and automation, hysteresis-based solutions are evolving to meet new challenges. Emerging trends include:
- Graphene-enhanced hysteresis discs for ultra-high temperature stability
- Self-learning dynamometers that adapt test protocols based on real-time AI analysis
- Blockchain-secured test data sharing across supply chains
A recent breakthrough saw a hysteresis clutch prototype achieve 99.8% energy recovery efficiency in regenerative braking systems—potentially adding 20 miles to EV ranges.
🛠️ **Choosing Your Partner in Precision**
Selecting hysteresis and motor testing solutions requires balancing technical specs with real-world pragmatism. Leading manufacturers now offer:
- Application-specific validation packages
- Cybersecurity-certified data management
- Carbon-neutral testing lifecycle programs
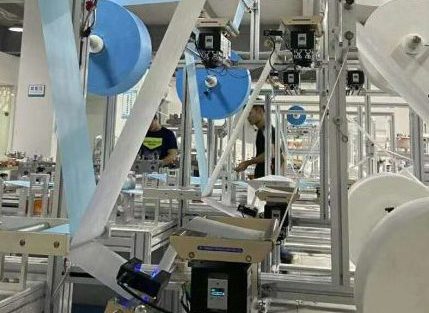
Pro tip: Look for suppliers offering virtual reality factory tours—it’s becoming the new standard for auditing equipment quality pre-purchase.
From the subtle whirr of a hysteresis brake ensuring your elevator stops exactly at floor level, to massive dynamometers stress-testing hypercar motors at 20,000 RPM, these technologies form the backbone of our electrified future. As you push the boundaries of what motors can achieve, remember: the right test equipment isn’t an expense—it’s the blueprint for unprecedented innovation.
🔧 **Final Thought:** In motorsport, they say races are won in the workshop. In today’s industrial arena, victories are forged in the test lab. With advanced hysteresis systems and intelligent motor testing solutions, you’re not just preparing for tomorrow’s challenges—you’re inventing them.